Automate 2023
tradeshowI attended the 2023 Automate show this past Monday and again enjoyed seeing much of the automation industry condensed into one hall. Alongside IMTS, there really is no other US-based event that does as good of a job of showcasing the variety conveyance, industrial robot, vision, control, and service providers as this show. And while Mechanomy focuses on the design side of manufacturing, the increasing flexibility of production is central to many of my considerations. It's also just fun to go and see different machines, designed for needs that I only vaguely imagine. Here are some of the cooler things I saw:
The Archimedes differential traction transmission
I was really excited to come across Innovative Mechatronic Systems' Archimedes Drive, even if I initially mistook it for SRI's Abacus concept. This transmission appears similar to a planetary gearhead in that there is a central input (sun) which drives a ring of planets that roll between the sun and an outer ring. The picture becomes more complicated when you see that none of the elements have gear teeth and that the planets have two differing radii:
Focusing on a planet roller, see 0:48 above, it has two cylindrical sections of differing diameter. The first diameter rolls on fixed bore of the housing, akin to the ring of a planetary gear, while the second rolls inside the output annulus. When their diameters equal, nothing happens, but when the diameters differ, even slightly, a large transmission ratio is developed.
While this concept could be implemented with regular gear teeth, the integer number of gear teeth will discretize and constrain the possible transmission ratios. Removing the gear teeth and simply relying on the contact friction of the rollers and internal cylinders, infinitely-many ratios may be created. The overview video mentions up to 10,000:1 and an input speed of up to 8000 rpm.
Without teeth, what maintains the input/output relationship? That is, it is usually significantly easier to put an encoder on the motor than on the transmission's output, and this arrangement can be trusted because the designer assumes that the gears will not skip teeth outside of failure. In the Archimedes this is managed by preloading the planet rollers to ensure that their contact friction is (likely appreciably) greater than that arising from the transmitted torque. Which is to say that as long as the application stays within the drive's rated torque, the drive will not slip. That said, my hazy recollection of tribology raises a suspicion that the drive will display error over very long rotations, and that this error may have some dynamic dependency. I suspect that this and other common apprehensions will be directly addressed with continued development. Already, their registration-gated brochure claims better speed, backlash, and stiffness than strain wave and planetary gears.
Naively, I'd expect these drives to have similar failure modes as roller and ball bearings, with generally dependable performance as long as contamination and thermals are handled. Their materials do not list any lifetime expectations at this moment.
As this is just their third show, their product release has a long way to go to get into the market. While targeting pick-and-place robots, likely Deltas and SCARAs, use in serial manipulators may take longer to achieve due to their greater degree of integration complexity. These would appear suitable for robot drive mechanisms, as they already expect wheel slippage, though at present their precision grinding may obstruct this market. The similarity to roller bearings is again suggestive that they may be able to significantly reduce their cost in time, and in ways that are not accessible to planetary and strain-wave gears.
RB9
RB9 is doing it, building a spatial cable robot for accessing large workspaces in generally warehouse or hangar applications. I phrase it that way because I find cable robots to be too captivating: they have a pretty large design space and they really obviously exhibit a wide range of classical dynamics, yet they also appear within the capability of a small team to design and produce. While they left the overall system at their hangar headquarters, I appreciated the drive unit they brought to the show and the wide-ranging discussion with their founder.
Airskin for Kuka
If you take a standard, non-collaborative robot arm and add instrumented cushions, does that make it safe to work next to without a cage? That's what Airskin is asking by attaching soft panels to regular robotic arms, each instrumented to detect collisions with unknown operators.
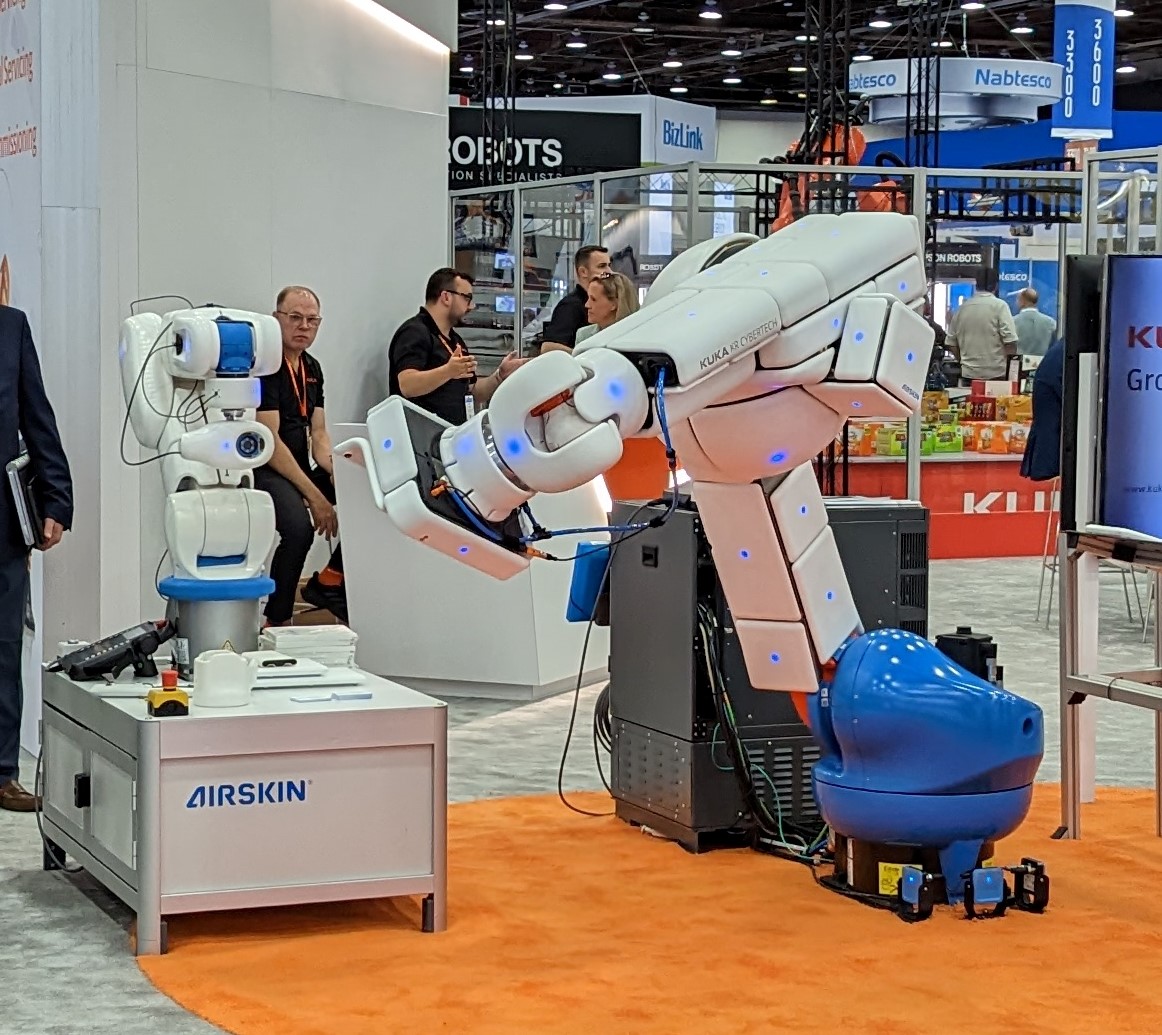
Unfortunately, the only people who can answer this are regulators and I'm not sure how many were in attendance or how easily convinced they may be.
Autonox Robotics
If anything, the trend of the last several years in industrial equipment has been to greater consolidation of ecosystems across the industry - whether that is motor+drive, motor+drive+controller, or across machines - despite the ever increasing programmability and decreasing cost of those motor drives.
So I was surprised to stumble across Autonox's booth and hear that they have found a number of customers who appreciate their modular, un-bundled approach. They design and produce the manipulator's mechanics, you (your integrator) bolt on your actuators and end-effectors and integrate it into the larger system.
The Henry Ford
My wife and I visited the Henry Ford museums prior to the show, and I am super impressed with the main museum. From "the oldest surviving steam engine in the world", an original Newcomen built in 1760, to Watt's 1796 pumping engine, across many engines used to power machines and buildings, to the portable steam engine that Henry Ford fixed, operated, and which launched his career in engines, to steam tractors and rail engines, and then to a large history of Ford vehicles and several notable planes, they have an excellent collection. They also have a number of historic machine tools and textile machines that would support a number of narratives about the nature of innovation.
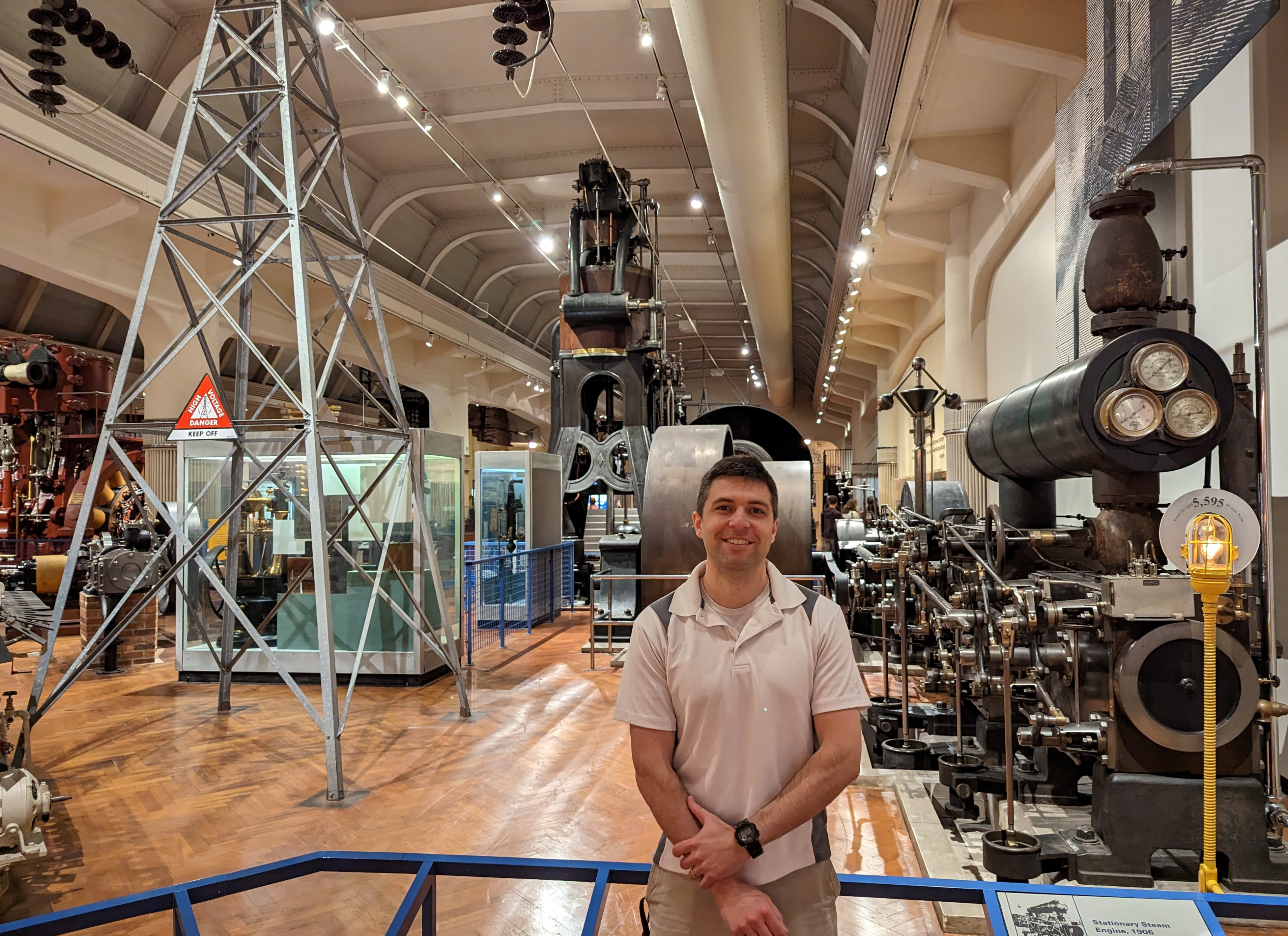
Two critiques: I would have liked the historical narratives to be much stronger and more personal, ideally through handouts of varying depth and focus. The majority of guests were clearly not understanding what they were seeing, and the overall exhibit could use much better signage to help you follow the progression. As it was, we started in the tractors and only slowly found the Newcomen at the rear of the exhibition. There was also no presentation of the motivating need for the various innovations, no attempt to show why these innovations were improvements on their predecessors. More than any specific invention, this desire to understand and solve needs is essential to any exploration of innovation.
Secondly, the museum only addressed Ford Motor Co and explicitly avoided the other car makers and broader industry. I found no mention of the significant resource booms Detroit set off in the Upper Peninsula and Minnesota. Similarly, while cursorily describing the assembly line the mechanical bits are frankly less innovative than the business and management systems that made them run. Including these would certainly expand the scope of the museum, but the hard part is the physical artifacts; everything else is just threading it together.
All-in-all, I'm looking forward to Automate 2024 in Chicago, hope to see you there!
— Ben Conrad
- Next: Validating product interest
- Previous: Modeling Fireball's Vise Hammer